Use of Soybean Oil like as Fuel for Diesel Cycle Engine
Ávila, M. T.; Gómez, L. C., Cabezas, L. M. C.; Souza, S. P.; Shrestha, D. S.
DOI 10.5433/1679-0375.2023.v44.48054
Citation Semin., Ciênc. Exatas Tecnol. 2023, v. 44: e48054
Abstract:
Diesel fuel price is rapidly increasing burdening the agricultural production costs. Additionally, diesel is contributing to a significant amount of life cycle greenhouse gases emissions. Strategically, using agricultural feedstock, such as soybean oil, will reduce fossil fuel price volatility and carbon footprint from agriculture. Although cheaper than biodiesel, use of pure soybean oil has shown to damage a regular diesel engine because of its high viscosity. In this work, a novel technology was developed and tested to overcome this problem by fueling a direct injection Diesel engine with refined soybean oil (edible oil) heated by engine coolant and exhaust gases. Thermal efficiency, air/fuel ratio, fuel injection timing, exhaust temperature and exhaust emissions were evaluated. The major finding of this study was to identify the feasibility of running a modified engine properly with heated soybean oil. The results showed that soybean oil use reduces emissions of nitrogen oxides, but contributes both to lower thermal efficiency and higher emissions of other products such as carbon monoxide and particulate matter compared to fossil diesel. Despite these negative results, solutions to reduce pollutant emissions are feasible.
Keywords: agribusiness, bioenergy, compression ignition engine, soybean oil
Introduction
The word ‘development’ can mean evolution, denoting a process of progressive change of the current conditions; the word ‘sustainable’ can express protection, avoiding the downfall of the conditions, either in the present or in the future. Therefore, sustainable development is often defined as manner of economic development that attends the present needs without compromising the capacity of future generations to supply their needs (Munn, 1992). Despite global ecological awareness, the reality still shows evident and continuous environmental degradation. Because energy plays an essential role in the development of the society, it is fundamental to recognize the importance of choosing more sustainable forms of energy.
The growing demand of fossil fuels and the limited easily exploitable oil reserves have contributed to the continuous increase of the oil price. With rising fossil fuel price comes the constant cost increase in supply chain. The agribusiness, for instance, is strongly impacted since it heavily depends on machines that consume diesel fuel. This strong dependency on diesel has considerably increased the agricultural sector expenses and, as consequence, has stimulated the use of renewable sources, like biomass, to produce alternative fuels (biofuels).
One possibility of replacing diesel is to utilize transesterified vegetable oils (fatty acid esters), commercially known as biodiesel. Biodiesel has great importance for having physical and chemical properties similar to the diesel fuel, not demanding changes in the engines. In spite of being an excellent alternative, biodiesel is more expensive than fossil diesel partly because of the cost of transesterification process that also requires a significant initial investment (Corsini et al., 2015).
Vegetable oils are cheaper than their respective esters. They are also easier to be obtained because the production of vegetable oil requires less processing (Falcon et al., 1985; Loos et al., 1985). Thus, the use of pure, non-transesterified vegetable oils in diesel engines is a desirable alternative to fossil diesel.
The first reference of using vegetable oil as fuel is from the beginning of the twentieth century. In the 1900 World´s Fair in Paris, Rudolf Christian Karl Diesel declared to the posterity: “In any case, it´s seem certain that the motor-power can still be produced from the heat of the sun, which always is available for agricultural purposes, even when all our natural stores of solid and liquid fuels are exhausted” (Knothe, 2001, p. 1104). Since that time, several experiments with different kinds of vegetable oil and their respective esters as fuel for diesel cycle engines have been realized.
Researchers in many countries have carried out experimental works using vegetable oils to replace traditional fuel of diesel cycle engines (A.S Ramadhas et al., 2004). Straight vegetable oil can be used as fuel in diesel engines with some minor engine modifications, playing an important role to reduce the environmental impact of fossil fuels. Results showed that running engine with vegetable oil had similar thermal efficiency, less power, higher particulate matter, and reduced nitrogen oxides (NOx) emission compared to diesel fuel. On the other hand, vegetable oil methyl esters performance and emission characteristics are comparable to diesel, what made them a good diesel fuel substitute.
Advantages of using straight vegetable oil include domestic production that would help to reduce petroleum imports; biodegradable and non-toxic; renewable fuel made from agricultural crops and waste; low aromatics and sulphur content; 80% heating value compared to diesel, reasonable cetane number, and enhanced lubricity.
However, technical difficulties with using straight vegetable oil were also reported like long term storage that affects fuel stability due to in oxidation and consequently engine performance and durability; material compatibility with some diesel engine components; and cold weather operations.
A common-rail turbocharged diesel engine fuelled with rapeseed oil, biodiesel and diesel fuel showed power loss (from 18 to 22%) from use of rapeseed oil and biodiesel at low loads, but at higher loads, the fuels had similar performance about 2800 rpm (Corsini et al., 2015). This behavior was attributed to the combined effects of density and viscosity of vegetable oils, electronic unit control, and injection timing (varied according to load). Opacity tests demonstrated the contribution of the biofuels in reducing soot formation and particulate emissions. Pollutant emissions are comparable to or lesser than those of diesel fuel, with exception of hydrocarbons (HC) emission from rapeseed oil that were higher.
Other study showed a decreasing trend for specific fuel consumption with load increasing in a direct injection Diesel engine (Bruno D’Alessandro et al., 2016). The study was conducted with different loads and fuel namely diesel, biodiesel, linseed oil, refined palm oil, five virgin vegetable oils (sunflower, palm, corn, soy and peanut) and two waste frying vegetable oils (sunflower and palm). Due to lower calorific values, specific biodiesel consumption was 14–15% higher and vegetable seeds oils consumption was 10–30% higher than diesel. Comparing fuel emissions, a decreasing carbon monoxide (CO) emission and an increasing nitrogen oxides (NOx) emission were observed with increasing load due to the higher combustion chamber temperatures caused by increased fuel injection confirmed by higher exhaust gases temperature. For biodiesel, exhaust gas temperature at higher loads was comparable to that of diesel, and at lower loads, it was higher than for diesel. With vegetable oils, exhaust gas temperature was often lower than that of biodiesel. Injector fouling caused by waste frying sunflower oil, refined palm oil and biodiesel was comparable to that of diesel. Soy, sunflower and peanut oils caused a medium grade fouling on the injectors, while corn and palm oils produced a medium–high grade fouling and carbonaceous deposits near the nozzles. Injector fouling caused by linseed oil was quite high.
A study was conducted to evaluate diesel performance and emissions of a 6 cylinder, turbocharged and after-cooled, direct injection Diesel engine with 10% and 20% volumetric blends of cottonseed oil, sunflower oil, cottonseed biodiesel and sunflower biodiesel (Rakopoulos et al., 2014). They found the fuel injection pressure diagrams and the ignition delay were almost the same for biofuel blends and neat diesel. With blends, the heat release rates were little delayed towards the final term of combustion, and cylinder temperatures were slightly reduced. The main contributions of biofuel use were:
Significant reduction of smoke opacity. Raw oils were better than their biodiesel counterpart and cottonseed oil performed better than sunflower;
Slight increase in nitrogen oxides (NOx) emissions. No difference between vegetable oils and biodiesel;
Increase of carbon monoxide emissions with the vegetable oil blends but decrease with biodiesel blends compared to diesel;
Increase of unburned hydrocarbon emissions. Higher increase for the vegetable oils than the corresponding biodiesel cases;
Engine brake thermal efficiency (fuel economy) with all biofuel blends practically the same as diesel fuel.
D. Subramaniam et al., 2013 found that the vegetable oil should not be used directly as fuel because of free fatty acids, phospholipids, sterols, water, odorants, and other impurities. To allow its use as fuel, the vegetable oil requires chemical modifications like transesterification, pyrolysis, and emulsification. In another study, Muralidharan & Vasudevan, 2011 analyzed the performance, emissions and combustion characteristics of a variable compression ratio engine fuelled with waste cooking oil biodiesel and diesel blends.
The experiments confirmed that the brake thermal efficiency, specific fuel consumption, brake power, exhaust gas temperature and mechanical efficiency of engine were a function of biodiesel blend, load and compression ratio.
Although use of straight vegetable oils as fuel for diesel cycle engines has demonstrated technical problems, relatively few experiments have been carried out to identify solutions to overcome the challenges of pure vegetable oils burning, searching for better and complete oxidation of them in diesel engines (Andrade, 1983; Falcon et al., 1983). This study aimed to adjust the viscosity of the soybean oil, one of the most common vegetable oil in the world, by changing the form of injection into the combustion chamber, to allow its application in compression ignition engines. It was used a double heating system characterized by two heat exchangers, installed before and after the injection pump, respectively, to supply the thermal energy (heat) required to reduce that viscosity. The direct injection engine was operated in laboratory to measure performance and emissions. All tests were performed with soybean oil and conventional diesel fuel as reference.
Material and methods
This research utilized a modified four-cylinder direct injection Diesel engine used in common tractors to perform routine agricultural operations, see Table 1.
Item | Description |
---|---|
Manufacturer | Perkins |
Model | AD4.248 (direct injection) |
Type | Four stroke diesel cycle |
Number of cylinders | Four, vertically assembled |
Coolant | Water driven by centrifugal pump |
Displacement | 4067.198 cm3 |
Bore | 100.965 mm |
Stroke | 127 mm |
Compression ratio | 16/1 |
Feeding | Diesel fuel driven by rotative injection pump (CAV) |
Injection timing | 23º before top dead center (bTDC) |
To address the high viscosity of the soybean oil for proper diesel engine operation, a special fuel heating system was installed jointed with the engine, aiming to take advantage of the energy of the cooling water and exhaust gases. The soybean oil heating system is shown schematically in Figure 1.
1 - Vegetable oil from the tank (25 °C) at atmospheric pressure;
2 - Slightly heated vegetable oil (70/80 °C) at atmospheric pressure;
3 - Slightly heated (70/80 °C) pressurised vegetable oil;
4 - Highly heated (about 150/200 °C) pressurised vegetable oil flowing to the injector the nozzle;
5 - Hot cooled from the engine;
6 - Slightly cooled coolant flowing to the radiator;
7 - Hot exhaust gases from the engine;
8 - Slightly cooled exhaust gases flowing to the exhaust pipe.
The soybean oil from the tank was heated to about 70 °C in a first stage by the engine coolant, Figure 2(a). This temperature was sufficient to reduce its viscosity from 37 cSt to 13 cSt according to Kern, 1987, so that it would not damage the injection pump by the high shear stresses of a very viscous fluid.
(a)
(b)
After being pressurized by the pump, the fuel passed through a second heating stage using the exhaust gases, Figure 2(b), that allowed the oil to reach higher temperatures (in the range of 150 – 200 ºC) and viscosities around 2.5 cSt or less. This second step implied in the change of properties such as viscosity, surface tension and volatility. In order to avoid excessive heating of the soybean oil, a butterfly type valve was installed in the exhaust duct. This valve allowed partial deviation of the exhaust gases directly to the atmosphere to enable a thermal transfer control of the exhaust gas heat exchangers.
The engine was coupled to an Eddy current dynamometer to collect the experimental data at 1200, 1400, 1600, 1800 and 2000 rpm for both fuels at full load, Figure 3. The engine was cold started with diesel fuel until the temperature at the exit of the injector nozzle reached 80 ºC. After this, the fuels were switched (at this temperature, the vegetable oil viscosity did not cause problem to the injection pump and the engine).
The fuel mass consumption was registered directly through the reservoir disposed on a digital scale that recorded the decrease in mass of the fuel in function of the demand imposed by the engine. The air consumption was measured using a "hot wire anemometer" calibrated through an orifice plate system. The anemometer was connected to the intake air duct. LabVIEW® program was used to collect data from both systems.
The torque was obtained from the dynamometer display that was calibrated using standard weights. The engine rotation was read by means of the dynamometer’s brake control device.
Several temperatures were collected using thermocouples, namely:
fuel temperature at the exit of the injection nozzle;
fuel temperature at the exit of the coolant heat exchanger (first heating step, just before the injection pump in the engine fueled with soybean oil);
exhaust gases temperature at the outlet of the exhaust manifold;
exhaust gases temperature at the exhaust heat exchanger outlet (in the soybean oil driven motor);
cooling water temperature at the head outlet;
crankcase oil temperature;
particulate matter flow temperature at the exhaust tip.
The particulate matter was collected by flowing part of the exhaust gases through a glass fiber filter installed in a flange produced specially to contain it. The collection time was fixed to 5 minutes and the filter was dried and weighted before and after collection process, with the differential value between the recorded weightings meaning the retained material.
The regulated pollutants (carbon monoxide - CO, carbon dioxide - CO2, hydrocarbons - HC and nitrogen oxides - NOx) and the residual oxygen (O2) were analyzed and quantified, as specified in Table 2, by sucking a small portion of exhaust gases expelled by the engine.
The injection pump, attached to the motor by three captive screws, allowed angular movement around its axis, what made possible to identify the optimal point for the engine operation throughout advance or delay of the injection point. Table 2 describes the instruments used during the experiments.
Item | Description |
---|---|
Measurement system of torque and rotational speed | Manufacturer: Schenck |
Model: W260 | |
Type: Eddy current ynamometer | |
Accuracy: 0.1 Nm; 1 rpm | |
Measurement system of time | Manufacturer: Sports Timer |
Accuracy: 0.01 s | |
Measurement system of temperature | Type: chromel-alumel thermocouple (K) |
Accuracy: 1º C | |
Measurement system of atmospheric conditions (temperature and pressure) | Manufacturer: Wilh. Lambrecht K. G. |
Type: thermometer/barometer | |
Accuracy: 1º C; 0.5 mm Hg | |
Measurement system of air consumption | Manufacturer: Bosch |
Type: hot wire anemometer | |
Accuracy: 0.1 g/s | |
Measurement system of fuel consumption | Manufacturer: Mettler Toledo |
Type: electronic scale wired to a computer | |
with LabVIEW program | |
Accuracy: 0.01 g/s | |
Measurement system of emission gases | Manufacturer: Tecnomotor |
Type: TM-131 analyser | |
Accuracies: CO - 0.01 %; CO2 - 0.1%; | |
HC - 0.01 ppm; NOx - 1 ppm; O2 - 0.01% | |
Results and discussion
Modified diesel engine fueled with heated soybean oil
The soybean oil temperatures reached above 150 ºC at the exit of the injectors, Figure 4, due to its heating by engine cooling water and exhaust gases in the heat exchangers, allowing the establishment of viscosities around 2.5 cSt, according to abacus found in Kern, 1987. These values are close to the standardized viscosity for fossil diesel, i.e., 2.7 cSt (Bruno D’Alessandro et al., 2016).
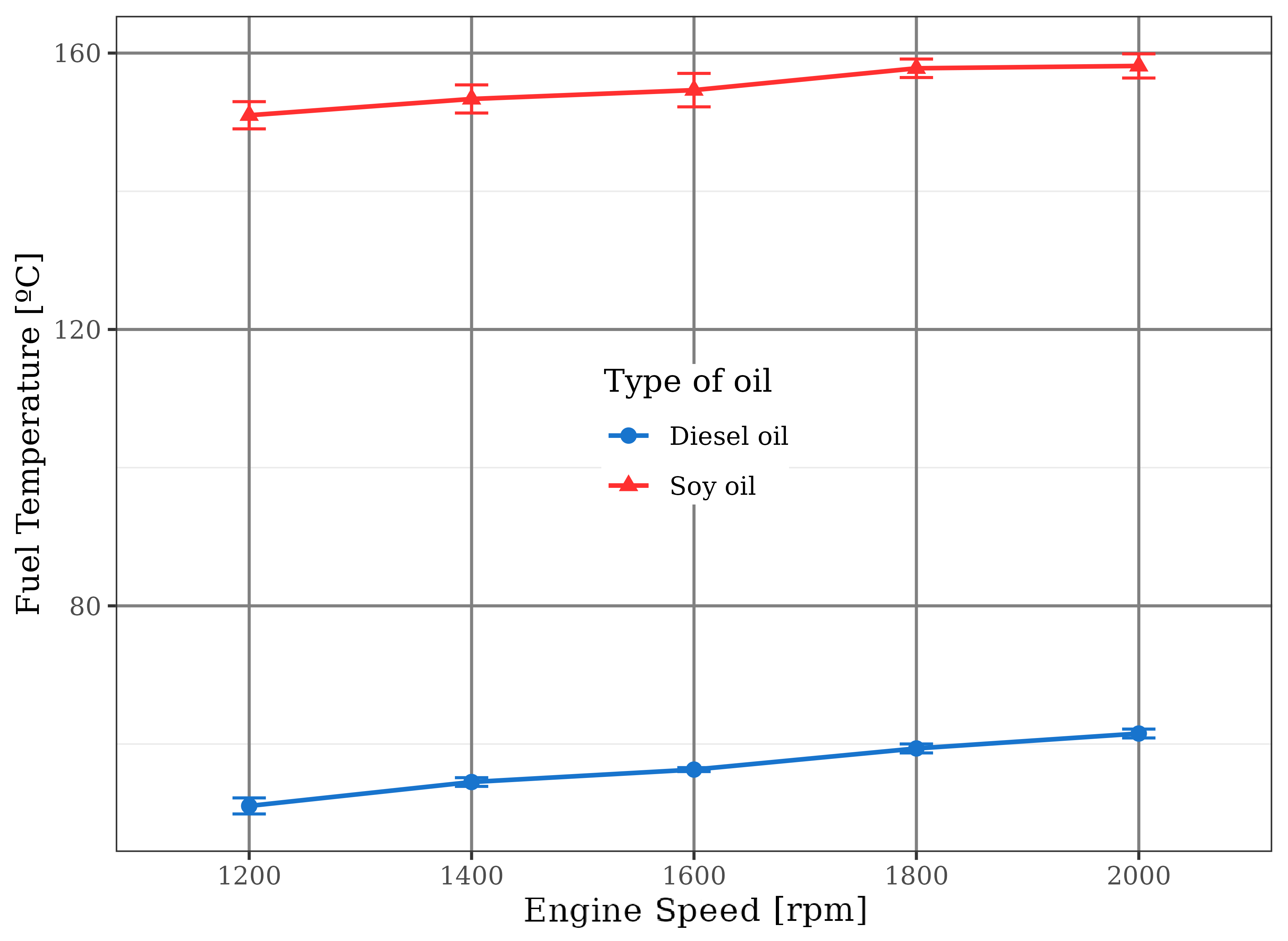
Consequently, the process of renewable fuel injection into the combustion chamber has been substantially improved by the suitability of the spray mechanism. This led to the fractionation of the fuel into small particles (droplets) for the formation of a favorable combustion air/fuel mixture, as expected. When the vegetable oil was heated, the described problems by literature disappeared, confirming the real contribution of this artifice to the injection and combustion processes by the beneficial interference in its viscosity. Venanzi et al., 1985 found that the use of a fuel with standardized value for this property influences positively the vaporization process inside the combustion chamber, the physical and chemical combustion delays, and the consequent formation of the chemical radicals.
Stoichiometric validation and adjustment
The replacement of diesel oil by vegetable oils leads the diesel engine to run with poorer mixtures when the fuel pump injection is not changed. This combustion process with excess of air causes invariably a torque reduction and a sensitive decrease in the black smoke emission - solid particles (Almeida, 1980).
The representative molecule of diesel fuel is n-cetane (hexadecane), expressed by the chemical formula C16H34 according to Pulkrabek, 1997. The stoichiometric combustion reaction of hexadecane with air is characterized by an air/fuel (AF) ratio equal to 14.9, according to equations (1) and (2):
(1)
C16H34+24.5O2+24.5(3.762)N2→16CO2+17H2O+24.5(3.762)N2
(2)
AF ratio=24.5×2×16+24.5×3.762×2×1416×12+34×1=14.9
On the other hand, vegetable oils are triglycerides formed from three acidic radicals (Almeida, 1980), represented generically by oleic acid, which generates the molecule of triolein (C57H104O6). Its reaction with atmospheric oxygen explains the burning stoichiometric value for this type of fuel, leading to an AF ratio equal to 12.4, according to equations (3) and (4):
(3)
C57H104O6 + 80 O2 + 80 (3.762) N2→ 57 CO2 + 52 H2 O + 80 (3.762) N2
(4)
AF ratio=80×2×16+80×3.762×2×1457×12+104×1+6×16=12.4
Therefore, it was decided to increase the injection pump flow rate (around 40%) to adjust the stoichiometry of the combustion when migrating from the fossil fuel to the renewable one. The aim was to increase torque and power in order to compensate the performance losses due to the lower calorific value of the soybean oil.
Figure 5 shows the air/fuel ratio behavior for the two fuels. The engine fueled with diesel worked at the stoichiometric operation point (equal to 14.9) or at slightly poor operation point. In case of the soybean oil, due to the 40% increase in the fuel discharge, the engine was operated with rich mixtures (air/fuel ratios lower than 12.4), with deleterious consequences on thermal efficiency and carbon monoxide emission.
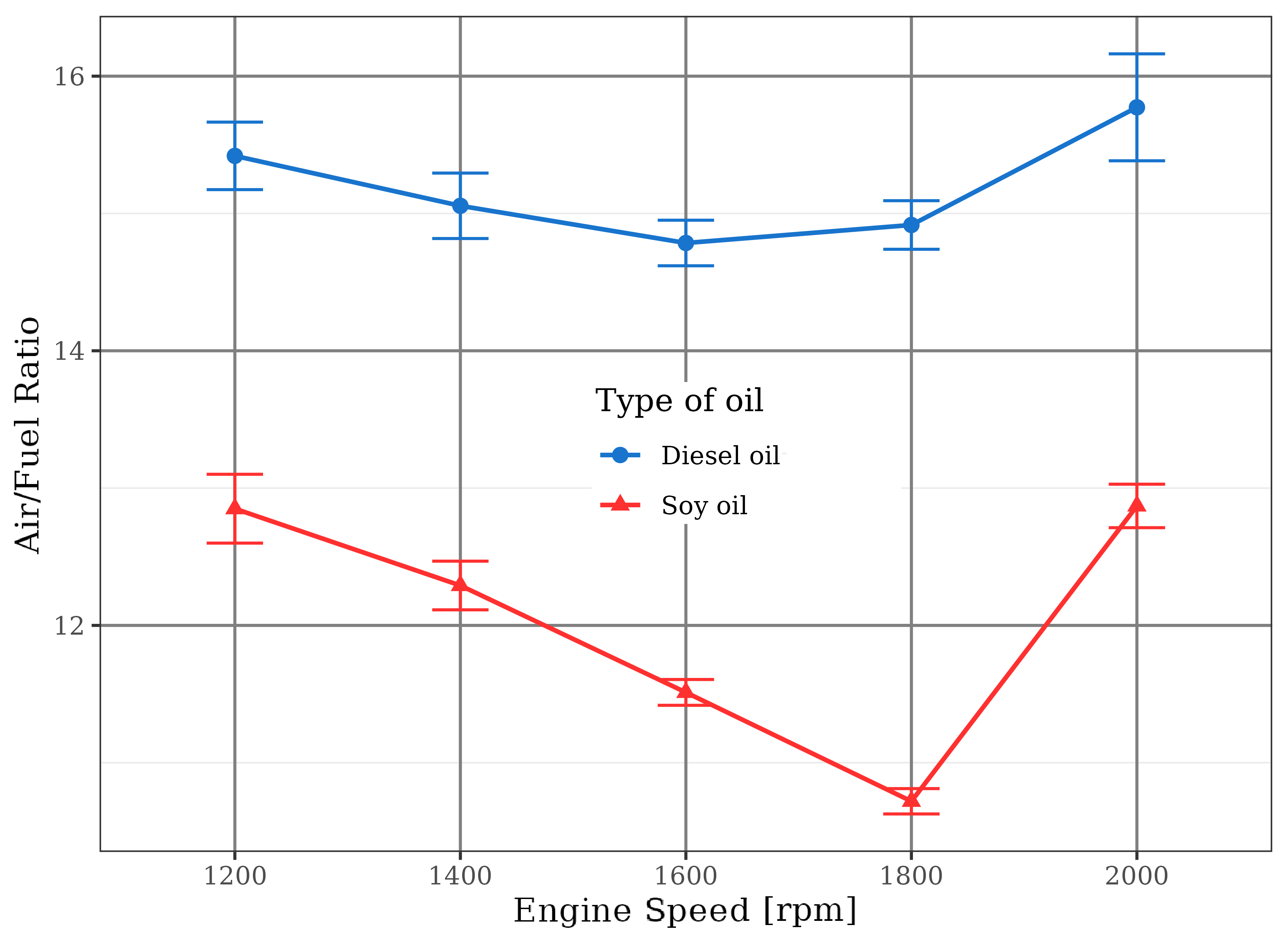
Torque
If the injection pump flow had not been changed for soybean oil, the air/fuel ratio would be reduced by the higher density of the vegetable oil compared to the diesel fuel, since the injected fuel volume would remain constant. Even so, poorer mixtures would be formed, leading to systematic reduction of the torque and less emission of pollutants related to the operation of the engine with excess air.
In order to increase the soybean fuel flow, the injection pump was modified, compensating the engine torque drop due to the use of vegetable oil. The corresponding curve to this higher fuel flow is shown in Figure 5. The direct effect on engine torque is plotted in Figure 6 that shows very similar performance of diesel engine when fueled with the two fuels. The soybean oil has 10% lower calorific value than diesel (Stern et al., 1983).
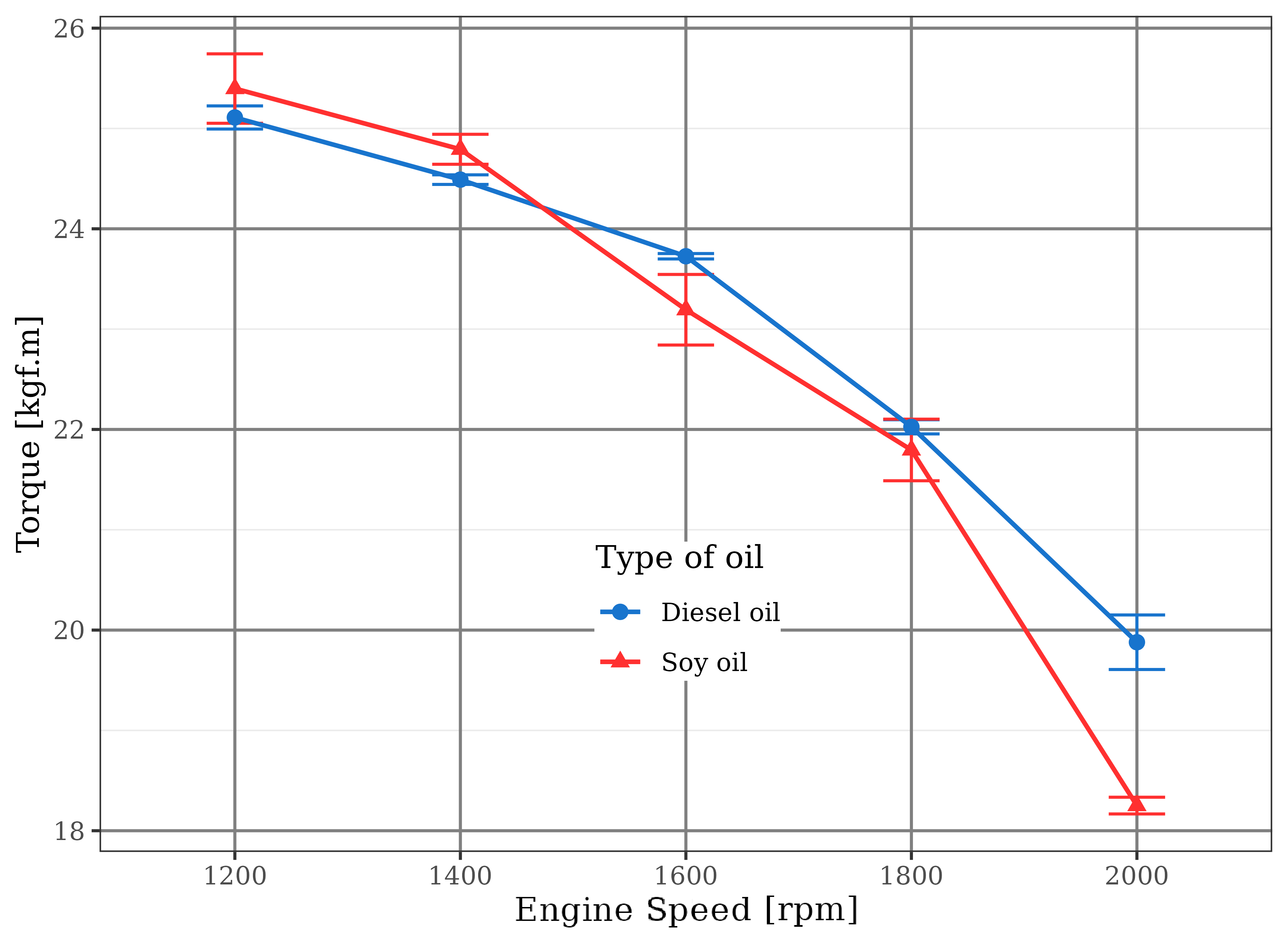
For maximum torque loss at 2000 rpm there was a reduction in the volume of soybean oil injected by the pump that operated at its maximum fuel flow limit. For both types of fuel, torque levels did not increase with rotation as the same rate as fuel consumption. This suggests that the shorter time available for the burning process inside the combustion chamber were not favorable to a fuel oxidation reaction for large-scale conversion of its chemical energy into mechanical work.
Fuel consumption and thermal efficiency
The engine thermal performance is always strongly influenced by the fuel discharge, i.e., the air/fuel ratio. According to Pulkrabek, 1997, the use of stoichiometric mixtures releases higher rates of heat, causing higher temperature peaks inside the combustion chamber and better rates of thermal efficiency.
Due to the increase of the injection pump’s discharge in the case of vegetable oil use, there was an augmentation of around 40% of its mass consumption in comparison to the fossil diesel, Figure 7. As mentioned before, air/fuel ratios lower than the stoichiometric point were used for soybean oil tests, resulting in almost 40% lower thermal efficiency at 1800 rpm compared to the diesel oil, Figure 8.


The increase of the injection pump’s discharge for soybean oil caused engine operation without excess air, eliminating from vegetable oil a very important feature: combustion amid wide oxygen availability. Therefore, the process of air/fuel mixture formation and the burning speed were impaired, with lower oxidation fuel and lower conversion of its chemical energy into work.
This condition generated two consequences: the increase in the torque was not proportional to the higher fuel flow rate and the combustion chamber temperature decreased due to the lower heat release. These aspects determined a lower thermal efficiency (on average, 20% lower) and a higher emission of pollutants, especially particulate material (black smoke).
One of the main reasons for this worse performance was the burning of rich mixtures, as previously commented. When the mixtures are poor, there is a great approximation of the so-called air standard (ideally, air-only motor) in which the specific heats vary little with temperature. This allows a small diminution of the isentropic coefficient value, leading to higher theoretical thermal efficiency values (Pulkrabek, 1997), according to equation (5):
η = 1 − 1r(k−1){(βk− 1)/[k (β − 1)]}, where η is the thermal efficiency, r stands for the compression ratio, k is the isentropic coefficient, and β means the cutoff ratio (positive volumetric variation during the combustion process).
Exhaust gases
Figure 9 shows that the temperature of the exhaust gases rose with the increase of the engine speed due to the greater energetic input caused by the greater fuel consumption. In addition, as already pointed out, the engine rotation increase diminished the available time for the development of a complete combustion process inside the chamber. This fact contributed to the exhaust temperature raising by the late burning of a fuel portion in the exhaust manifold after exhaust valve opening.

A comparison of the application of the two fuels showed lower exhaust temperatures in case of the diesel due to combustion of poor mixtures and more complete burning at the beginning of the expansion stroke. This second aspect is result of appropriate properties of the fuel like as viscosity and volatility, which guaranteed good atomization in the injection process, small ignition delay and rapid heat release to be transformed into mechanical work. Thus, in the case of diesel fuel, when the exhaust valve was opened, the temperature of the exhaust gases had already decreased considerably.
With soybean oil, the presence of rich mixtures did not allow full oxidation of its molecules. In this case, a lower heat release for the mechanical work production occurred in the expansion stroke. In addition, it was observed a larger amount of fuel that burned in the exhaust manifold, increasing the temperature of the exhaust gases and the emission of pollutants, especially particulate matter. Specifically at the engine speed of 2000 rpm, when the temperature of the exhaust gases exceeded 650 ºC, it was noticed that the exhaust manifold became incandescent, denoting great loss of fuel enthalpy and low thermal efficiency.
As stated earlier, the injection pump was handled to increase the soybean oil discharge and the torque production. Thus, the rich mixtures with soybean oil made that the combustion process occurred amid oxygen shortage, the opposite of diesel oil combustion that was always performed with air excess. This behavior is shown in Figure 10 that demonstrates that the diesel fuel engine discharged more oxygen than the soybean oil engine.
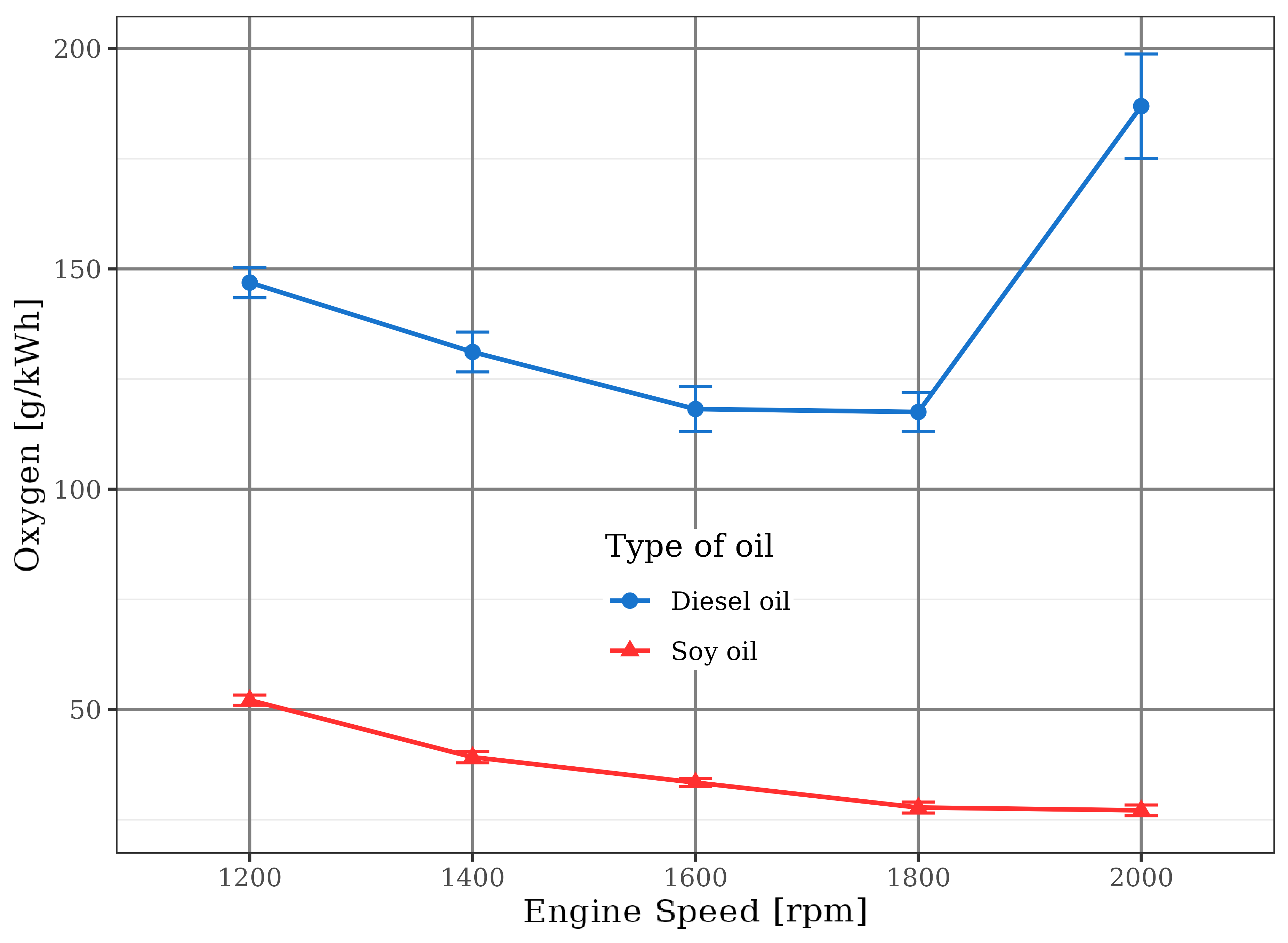
This fact triggered a large emission of carbon monoxide (CO) and total hydrocarbons (HC) by using soybean oil. In this situation, a partial oxidation of the fuel happened because there was not sufficient oxygen to react with carbon and hydrogen present in the fuel to convert it into carbon dioxide and water. This trend is observed in Figures 11 and 12.
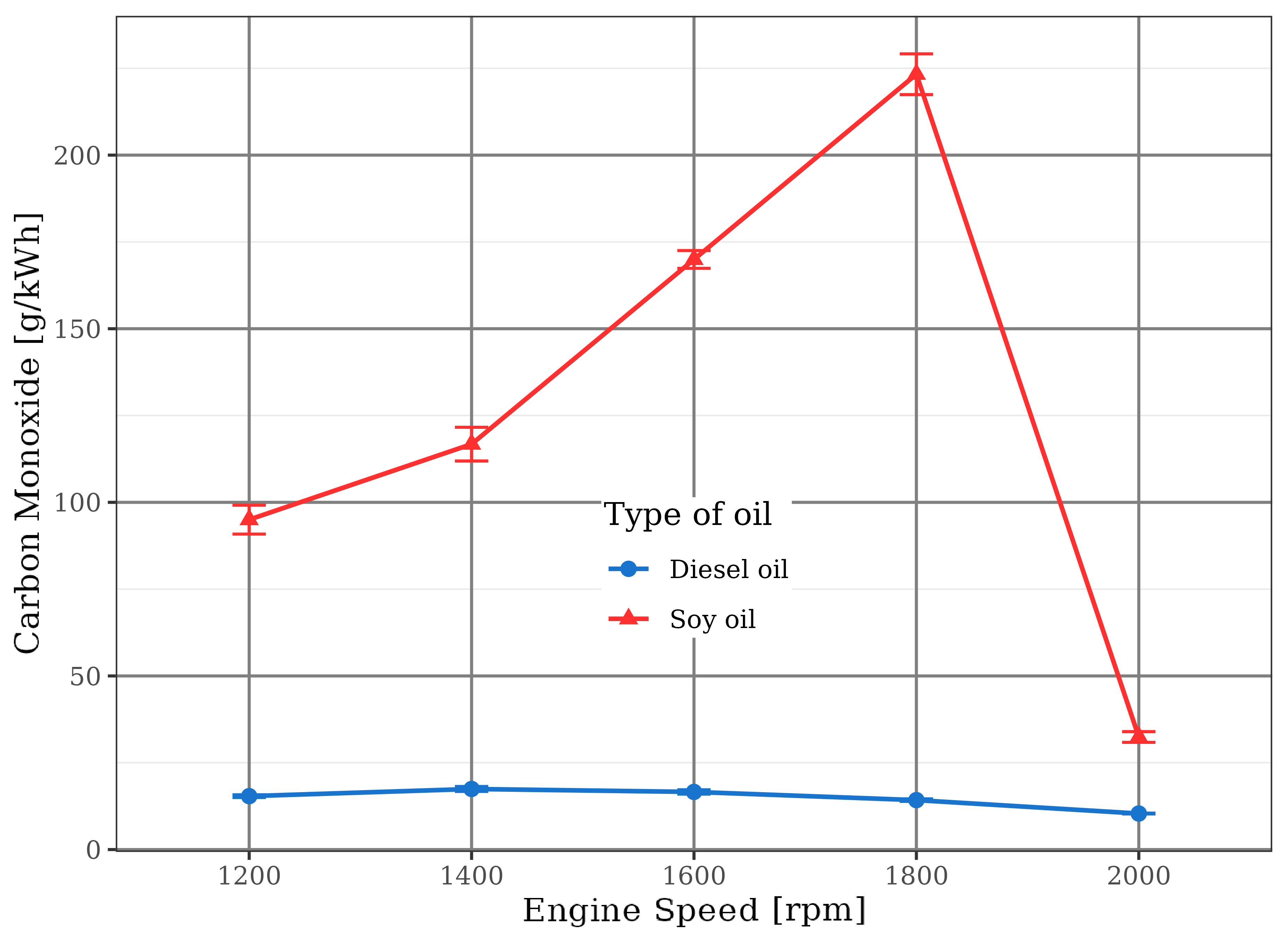
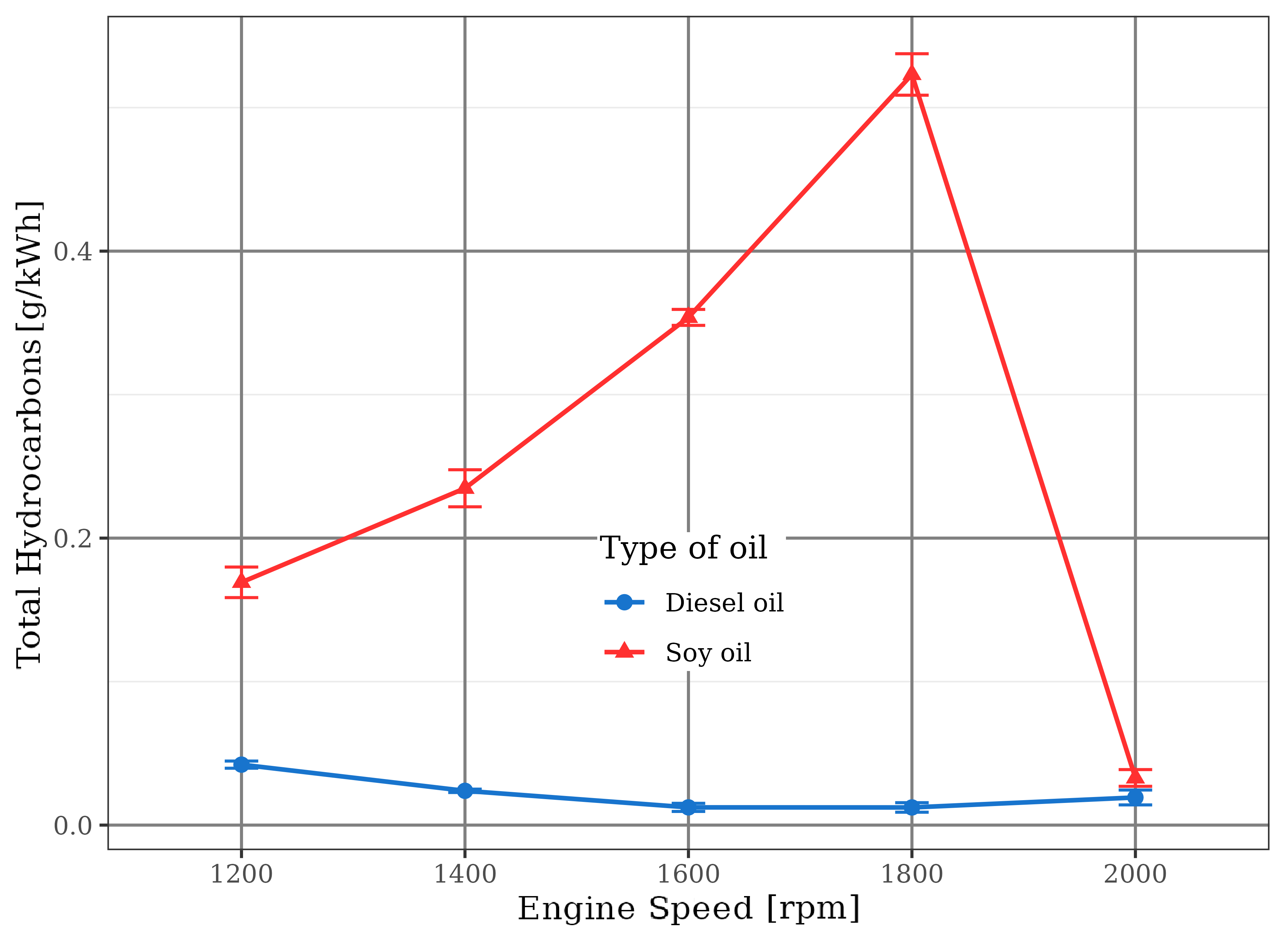
In the case of diesel oil, the emission of these gases was kept very small by the burning at stoichiometric or slightly poor mixtures (with up to 10% excess air), in direct agreement with literature information (Pulkrabek, 1997) that highlighted very low CO and HC rates in combustion of poor mixtures, especially those with 20% excess air. Even in these types of mixtures, there is some hydrocarbon emission due to their heterogeneity, which means that some fuel molecules do not find all the necessary oxygen for a complete combustion reaction.
Another explication can be based in the undesirable cooling of the flame front caused by its contact with cylinder walls, and by the expansion stroke that causes pressure and temperature reductions, what leads to burning failure in some portions of the fuel and slower combustion process (Pulkrabek, 1997).
In this context, the use of soybean oil, with low volatility, aggravated this phenomenon by recondensation of part of fuel that was vaporized in the initial stage of the combustion, droplet collision with internal walls of the engine, polymerization, and incomplete burning by more complex combustion than in the case of diesel fuel (Almeida, 1980).
On the other hand, there is a specific point in Figures 11 and 12 related to the operation of the soybean oil engine at the 2000 rpm. In this speed, the injection pump has suffered an automatic flow cut because it was already operating in its maximum possible discharge. Under these conditions, the mixture within the combustion chamber reached the stoichiometric condition, leading to drastic reductions in CO and HC emissions that were close to the values of diesel fuel engine. Nevertheless, stoichiometric or slightly poor mixtures produced some CO due to their characteristic heterogeneity, with some rich portions that induced incomplete burn. This behavior is more significant for the motor driven by soybean oil, probably due to the presence of the fuel polymerization phenomenon that hindered its complete oxidation.
In relation to the carbon dioxide (CO2), a more efficient combustion process determined a higher formation of this gas, as can be seen in Figure 13. This specific condition denoted a more complete burning process of the soybean oil (oxygenated fuel) characterized by the fact that a large part of the carbon was oxidized to carbon dioxide and a considerable portion of hydrogen was transformed into water vapor.

The nitrogen oxides (NOx) values are displayed in Figure 14. The use of soybean oil did not allow the combustion chamber to reach as high temperatures as verified in the diesel fuel engine. Lower combustion temperatures, combined with air/fuel ratios smaller than the stoichiometric point, always contributes to lower nitrogen oxides emissions (Pulkrabek, 1997). These conditions were the reason for the lower level of NOx emission by the soybean oil engine, even though the oxygen content of the renewable fuel was considerable - between 10% and 15%, by mass, according to Almeida (1980).
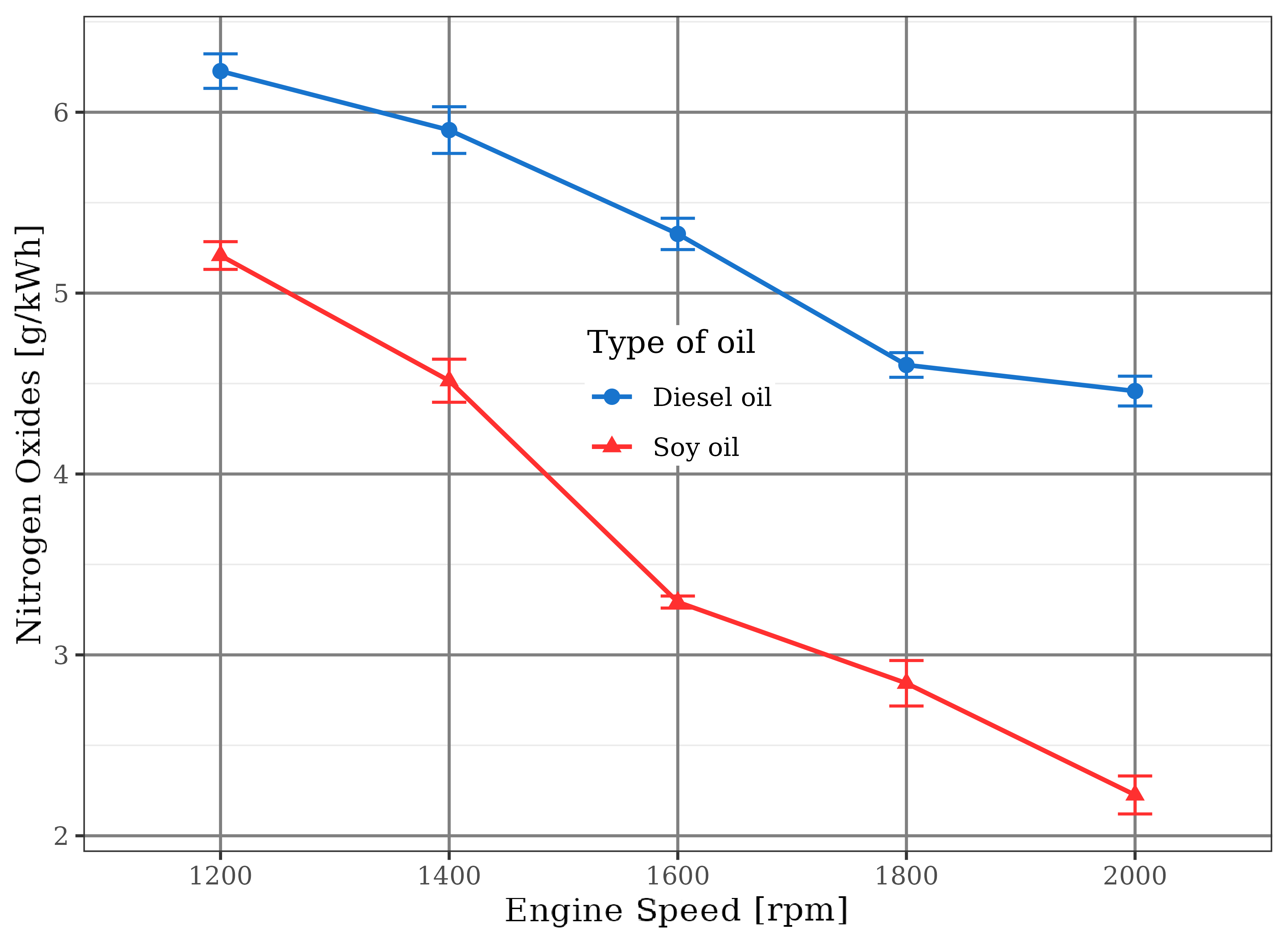
Particulate material emission of the vegetable oil engine were higher because of the use of rich mixtures, Figure 15. At speeds in which the soybean oil/air mixture was closer to the stoichiometric value, the higher particulate emission was linked to the insufficient time for the complete oxidation of the carbon to CO2 inside the combustion chamber. This behavior led to the exhaust gases temperature increase by the late burning of the remaining fuel in the exhaust manifold and to the reduction in the thermal efficiency.
It is important to note that the operation of compression ignition engines in the stoichiometric range usually generates excessive levels of particulate emissions, which is highly attenuated by the use of poor mixtures, with air excess (Pulkrabek, 1997).

Injector fouling
In spite of the substantial decrease in the viscosity of the soybean oil due to its heating in the heat exchangers (cooling water and exhaust gas), which also contributed to increase its volatility, strong polymerization of the injector nozzles was observed, Figure 16.
(a)
(b)
As the engine used in the experiments was remanufactured but not previously operated and was not disassembled after the tests, it was supposed the same damages were occurred with the pistons, inlet and exhaust valves, head and cylinders. This deleterious effect is related to the polyunsaturated feature of the soybean oil, mainly constituted by linoleic acid that presents two molecular unsaturations, and by linolenic acid with three double bonds in its molecule (Ma & Hanna, 1999). These chemical structures facilitate the rapid degradation of vegetable oil by atmospheric oxygen, generating varnishes (polymer compounds) that are carbonized almost instantly by the high temperatures in the combustion chamber.
Conclusions
It was possible to operate compression ignition engines with heated pure soybean oil. It was concluded that:
the use of vegetable oil demanded the increase of injection pump discharge in order to maintain the same level of mechanical performance (torque);
the higher fuel discharge of soybean oil eliminates any possibility of engine operation with excess air, causing deleterious effects about thermal efficiency and emission of some regulated pollutants;
due to the burning of rich mixture, the engine fueled with soybean oil was operated frequently with low oxygen availability, what caused excessive emissions of carbon monoxide (CO) and hydrocarbons (HC). At 2000 rpm, when the air/soybean oil mixtures approached the stoichiometric value, CO and HC levels were reduced, becoming close to those related to the fossil diesel;
carbon dioxide (CO2) emissions decreased with increasing of CO and HC emissions, proving the deficient oxidation of carbon and hydrogen in both fuels (diesel and soybean oil);
nitrogen oxides (NOx) emissions of soybean oil were smaller than diesel, showing that combustion temperatures were lower because of incomplete vegetable oil oxidation in function of its chemical feature and rich mixtures;
more particulate matter was produced with soybean oil because of the rich mixture’s combustion; at 2000 rpm, when the air/fuel ratio approached the stoichiometric value, the high levels of particulate matter were maintained by the insufficient time for complete carbon oxidation to CO2 into the combustion chamber;
in spite of soybean oil heating to reduce its viscosity, hard injector nozzle polymerization, in spite of the soybean oil heating to reduce its viscosity, hard injector nozzle polymerization (caused by the polyunsatured feature of the vegetable oil) was observed.
The increment of pollutant emissions during the experiments proved that soybean oil was not feasible considering the specific engine used in the tests. A possible solution for this problem might be the application of turbo-charging with a secondary fuel, like as ethanol, with favorable properties. The realization of further investigations should contribute to increase the use of renewable fuels in internal combustion engines, with positive effects in the environment.
Author contributions
M.T. Ávila participated in the: Conceptualization, Data Curation, Funding Acquisition, Research, Methodology, Project Management, Validation, Visualization, Writing – Original Draft, Revision and Editing.L.C. Gómez participated in the: Resources, Supervision, Visualization, Writing – Original Draft. L.M.C. Cabezas participated in the: Formal Analysis.S.P. Souza and D.S. Shrestha participated in the:Writing – Original Draft.
Conflicts of interest
The authors certify that there is not a commercial or associative interest that represents a conflict of interest in relation to the manuscript.
Acknowledgments
The authors would like to thank H.J.D. Trebi and R.A. Lourenço by the assistance on the experimental bench where the engine was tested.
References
Almeida, S. J. (1980). Alternative source of energy by use of vegetable oils in compression ignition engine .
Andrade, J. M. V. (1983). An overview about vegetable oils as alternative fuels. In Proceedings [Symposium]. 1st Symposium of Automotive Engineering. Brasília, Brazil.
Corsini, A., Marchegiani, A., Rispoli, F., Sciulli, F. & Venturini, P. (2015). Vegetable oils as fuels in Diesel engine. Engine performance and emissions. 942 - 949. https://doi.org/10.1016/j.egypro.2015.12.151
Bruno D’Alessandro, Gianni Bidini, Mauro Zampilli, Paolo Laranci, Pietro Bartocci & Francesco Fantozzi (2016). Straight and waste vegetable oil in engines: Review and experimental measurement of emissions, fuel consumption and injector fouling on a turbocharged commercial engine. 198-209. https://doi.org/10.1016/j.fuel.2016.05.075
Falcon, A. M., Fernandes, F. R. & Pischinger, G (1983). Use of alternative fuels based in vegetable oils in direct and indirect injection Diesel engines. In Proceedings [Symposium]. 1st Symposium of Automotive Engineering. Brasília, Brazil.
Falcon, A. M., Fernandes, F. R. & Pischinger, G (1985). Use of diesel oil ‘in nature’ added to pure vegetable oils in direct injection Diesel cycle engines. In Proceedings [Symposium]. 2nd Symposium of Automotive Engineering. Brasília, Brazil.
Kern, D. Q (1987). Heat transfer processes. Guanabara Dois S.A.
Knothe, G. (2001, p. 1104). Historical perspectives on vegetable oil-based diesel fuels. 1103 - 1107.
Loos, E. A., Nobre, J. I. T. & Stivi; J. (1985). Blends of diesel and vegetable oils as fuel of Diesel cycle engines. In Proceedings [Symposium]. 2nd Symposium of Automotive Engineering. Brasília, Brazil.
Ma, F. & Hanna, M.A. (1999). Biodiesel production: a review. 1-15.
Munn, R. E. (1992). Towards sustainable development. 70(15A), 2725 - 2731.
Muralidharan, K. & Vasudevan, D. (2011). Performance, emission and combustion characteristics of a variable compression ratio engine using methyl esters of waste cooking oil and diesel blends. 3959 - 3968. https://doi.org/10.1016/j.apenergy.2011.04.014
Pulkrabek, W. W. (1997). Engineering fundamentals of the internal combustion engine. Prentice Hall.
Rakopoulos, D. C., Rakopoulos, C. D., Giakoumis, E. G., Dimaratos, A. M. & Kakaras, E. C. (2014). Comparative Evaluation of Two Straight Vegetable Oils and Their Methyl Ester Biodiesels as Fuel Extenders in HDDI Diesel Engines: Performance and Emissions. 140(3), 1-11. https://doi.org/10.1061/(ASCE)EY.1943-7897.0000137
A.S Ramadhas, S Jayaraj & C Muraleedharan (2004). Use of vegetable oils as I.C. engine fuels: A review. 727-742. https://doi.org/10.1016/j.renene.2003.09.008
Stern, R., Guibet, J. C. & Graile, J. (1983). Les huiles végétales et leurs dérivés: carburant de substitution (analyse critique). 38(1), 121-136. https://doi.org/10.2516/ogst:1983008
D. Subramaniam, A. Murugesan, A. Avinash & A. Kumaravel (2013). Bio-diesel production and its engine characteristics—An expatiate view. 361-370. https://doi.org/10.1016/j.rser.2013.02.002
Venanzi, D., Santos, A. M. & Cardoso, S. (1985). Alternatives of ethyl alcohol use in diesel engines. In Proceedings [Symposium]. 2nd Symposium of Automotive Engineering. Brasília, Brazil.